Discover What is Porosity in Welding and Its Effect on Architectural Integrity
Wiki Article
The Scientific Research Behind Porosity: A Comprehensive Guide for Welders and Fabricators
Recognizing the detailed devices behind porosity in welding is important for welders and makers striving for flawless craftsmanship. From the structure of the base products to the complexities of the welding procedure itself, a wide variety of variables conspire to either exacerbate or relieve the presence of porosity.Recognizing Porosity in Welding
FIRST SENTENCE:
Evaluation of porosity in welding discloses vital insights right into the integrity and top quality of the weld joint. Porosity, defined by the visibility of cavities or voids within the weld steel, is a typical issue in welding processes. These gaps, if not correctly attended to, can endanger the structural integrity and mechanical buildings of the weld, bring about possible failings in the completed product.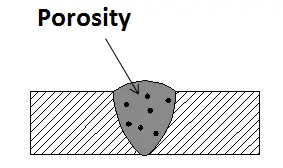
To identify and measure porosity, non-destructive screening methods such as ultrasonic testing or X-ray assessment are frequently utilized. These strategies allow for the identification of inner flaws without compromising the honesty of the weld. By examining the size, form, and distribution of porosity within a weld, welders can make informed choices to enhance their welding processes and achieve sounder weld joints.

Aspects Influencing Porosity Development
The event of porosity in welding is influenced by a myriad of variables, ranging from gas protecting efficiency to the details of welding parameter setups. One essential variable adding to porosity development is insufficient gas securing. When the shielding gas, normally argon or carbon dioxide, is not efficiently covering the weld pool, climatic gases like oxygen and nitrogen can pollute the liquified metal, leading to porosity. In addition, the tidiness of the base products plays a considerable function. Impurities such as rust, oil, or wetness can vaporize throughout welding, creating gas pockets within the weld. Welding criteria, consisting of voltage, present, travel speed, and electrode kind, additionally effect porosity formation. Using inappropriate setups can produce extreme spatter or warmth input, which subsequently can cause porosity. The welding method utilized, such as gas metal arc welding (GMAW) or shielded metal arc welding (SMAW), can affect porosity development due to variants in warmth circulation and gas coverage. Comprehending and regulating these variables are vital for decreasing porosity in welding procedures.Effects of Porosity on Weld High Quality
The existence of porosity likewise weakens the weld's resistance to rust, as the caught air or gases within the spaces can react with the surrounding environment, leading to deterioration over time. find out here Additionally, porosity can prevent the weld's ability to endure stress or effect, additional endangering the overall top quality and dependability of the bonded structure. In critical applications such as aerospace, auto, or structural building and constructions, where security and sturdiness are paramount, the damaging effects of porosity on weld top quality can have serious effects, emphasizing the navigate to this site relevance of reducing porosity via proper welding strategies and treatments.Techniques to Decrease Porosity
To improve the top quality of welded joints and make certain architectural stability, welders and makers utilize specific techniques intended at reducing the formation of gaps and dental caries within the material throughout the welding process. One reliable method to lessen porosity is to make certain appropriate material preparation. This consists of thorough cleansing of the base steel to eliminate any type of impurities such as oil, grease, or dampness that could add to porosity development. In addition, using the suitable welding criteria, such as the correct voltage, present, and take a trip rate, is essential in avoiding porosity. Maintaining a regular arc size and angle during welding also assists minimize the chance of porosity.
Furthermore, selecting the appropriate securing gas and maintaining proper gas flow rates are essential in decreasing porosity. Making use of the appropriate welding technique, such as back-stepping or using a weaving activity, can additionally aid distribute warmth equally and lower the possibilities of porosity formation. Finally, making sure correct air flow in the welding atmosphere to get rid of any kind of prospective sources of contamination is important for accomplishing porosity-free view publisher site welds. By applying these methods, welders can efficiently reduce porosity and create premium welded joints.
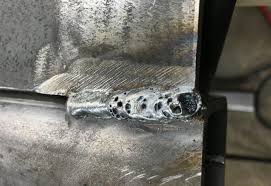
Advanced Solutions for Porosity Control
Executing advanced technologies and cutting-edge approaches plays an essential function in attaining exceptional control over porosity in welding processes. One innovative remedy is the usage of advanced gas mixes. Shielding gases like helium or a blend of argon and hydrogen can aid minimize porosity by offering better arc security and enhanced gas protection. Furthermore, employing sophisticated welding techniques such as pulsed MIG welding or customized atmosphere welding can additionally help alleviate porosity concerns.One more innovative remedy involves the use of advanced welding tools. As an example, using devices with integrated attributes like waveform control and advanced power resources can improve weld quality and minimize porosity threats. The application of automated welding systems with precise control over criteria can considerably lessen porosity flaws.
Moreover, integrating sophisticated surveillance and evaluation innovations such as real-time X-ray imaging or automated ultrasonic testing can help in discovering porosity early in the welding procedure, permitting immediate corrective activities. Overall, integrating these advanced solutions can substantially improve porosity control and improve the general high quality of welded elements.
Conclusion
In verdict, recognizing the scientific research behind porosity in welding is important for welders and makers to generate high-grade welds. By determining the factors influencing porosity development and carrying out methods to reduce it, welders can boost the overall weld high quality. Advanced services for porosity control can further enhance the welding process and make certain a solid and reputable weld. It is important for welders to continuously educate themselves on porosity and execute ideal methods to achieve optimum outcomes.Report this wiki page